If you have coated your tools in the past, there has likely been some wear on the coating, reducing its film thickness. While Carbon Coat is very hard, it relies on that film thickness to be effective. Eventually, Carbon Coat will wear down, leaving your tools susceptible to corrosion. The key to long-lasting protection is to reapply before you see any corrosion. Taking this approach allows Carbon Coat to continue to be the most effective, low-effort solution for cast iron maintenance.
What to Do
If you have coated your tools in the past, the easiest way to keep them protected is to refresh the coating by adding a few new layers of Carbon Coat. This is a very quick and easy process. Simply follow these steps:
- Thoroughly decontaminate the surface with 2-3 applications of Carbon Cleanse. Carbon Cleanse will remove any waxes, oils, sap, Carbon Glide, etc., that may be on the surface of the tool.
- Apply 2-3 new layers of Carbon Coat, making sure to wait an hour between each layer.
- Allow the surface to cure for 24-48 hours.
- Spray down some fresh Carbon Glide and put the tool back to work.
The whole process is quick and easy and will yield long-lasting results. In fact, as you continue to maintain the coating, adding new layers increases the film thickness, resulting in increased protection and effectiveness over time.
What to Do If You Are Already Seeing Corrosion
- Remove corrosion spots by hand with our Abrasive Pads; first with a maroon pad, then once the corrosion is removed, switch to a gray abrasive pad, and follow up with a white abrasive pad on those areas.
- Spot treat those areas with Carbon Coat. Take a coating cloth, cut it into four pieces, fold one piece into a small coating applicator, and apply Carbon Coat to the small areas. Make sure to wear gloves. Apply 2-3 layers, waiting an hour between each layer to build a film.
- At this point, you can follow the steps above, or you can attach a white pad to your random orbital sander and briefly go over the entire surface to even out the appearance before moving to the steps mentioned above.
Pro Tips
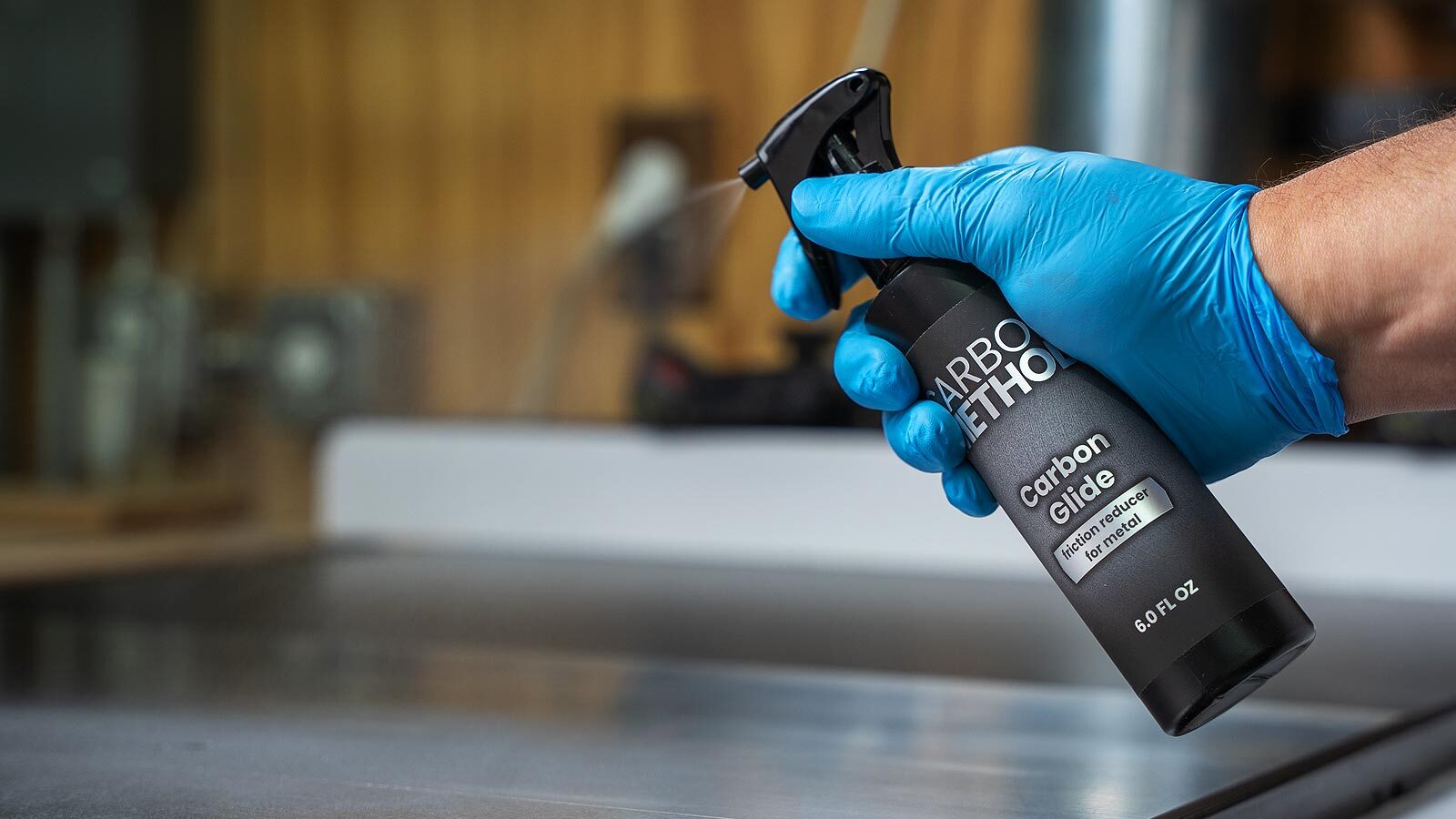
Easy Glider
Regular applications of Carbon Glide will not only add protection and make your tool surfaces really slick but will also act as a wear layer. Regular applications of Carbon Glide will extend the life of Carbon Coat by wearing the Carbon Glide layer instead of the Carbon Coat.

Harsh Environmentalism
In harsh environments (non-climate-controlled shops, or areas of high humidity and/or rain), applying more layers of Carbon Coat upfront will yield major benefits. We have seen drastic improvements in longevity and effectiveness with 5 or even 6 layers of Carbon Coat. A thicker film of Carbon Coat yields more cross-linking bonds and more material to wear against before the risk of corrosion.
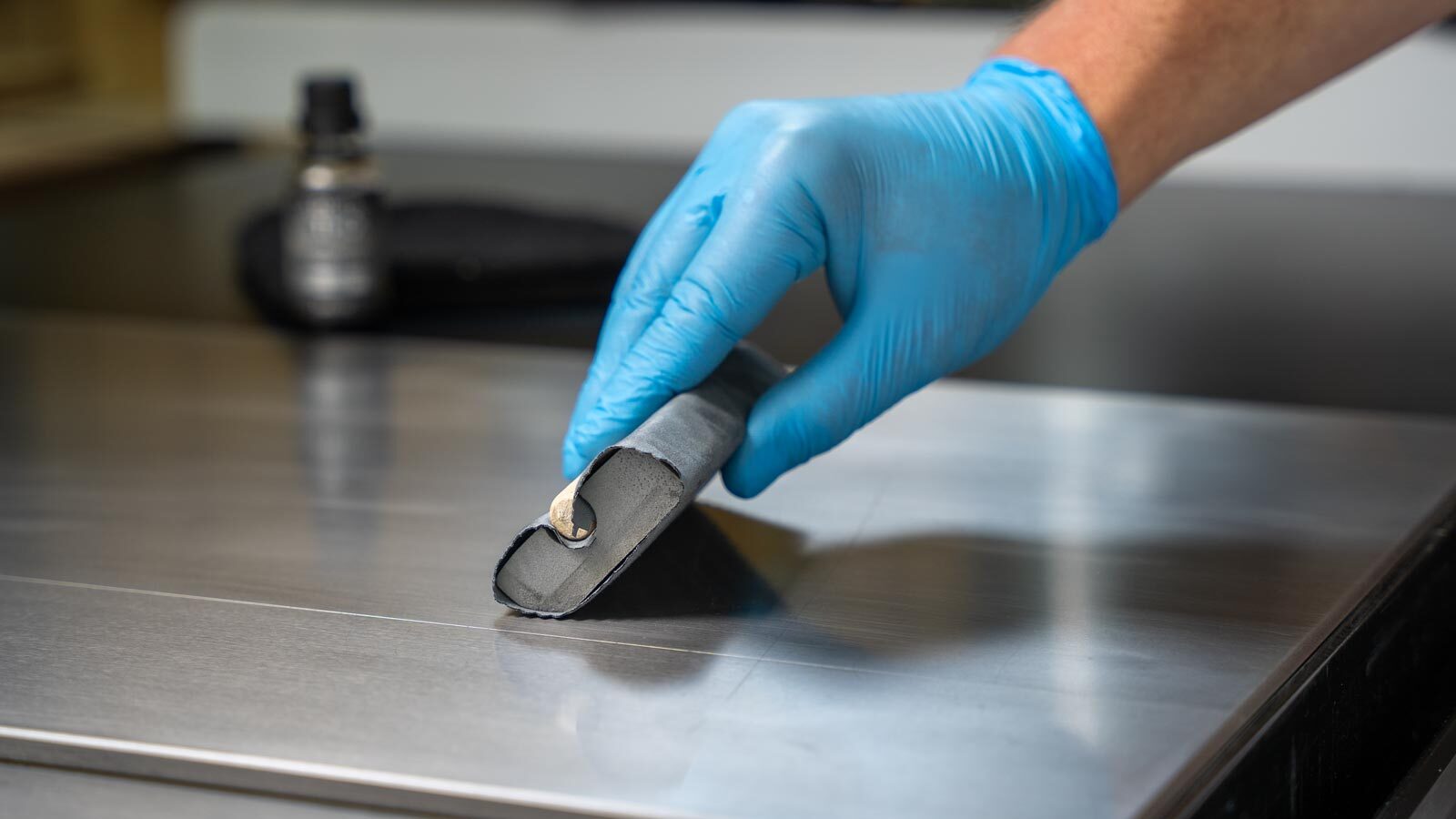
Timing is Everything
Remember to wait a full hour between layers of Carbon Coat. This is the most frequently missed step and unfortunately it is detrimental to the longevity of Carbon Coat. By waiting an hour between layers, the previous layer has time to film. Carbon Coat requires layers stacking on top of each other to be effective. If that film has not formed, the previous layer will rewet and the new layer applied will simply buff off. So remember: waiting an hour between layers is one of the most important steps to our process.
Conclusion
Carbon Coat is a major advancement in cast iron protection, but it isn't actually magic - no matter what you've heard! Carbon Coat will wear over time, and as it wears, it will lose effectiveness, leaving your cast iron vulnerable to corrosion. This is why refreshing Carbon Coat with a few new layers will keep your tools in top shape and rust-free. The key is to refresh before you see any corrosion, resulting in the lowest-maintenance approach to cast iron protection available anywhere.